Business
Biggest Recycling Plant to Tackle Electric Vehicle Battery Waste in the US is Now Open for Business
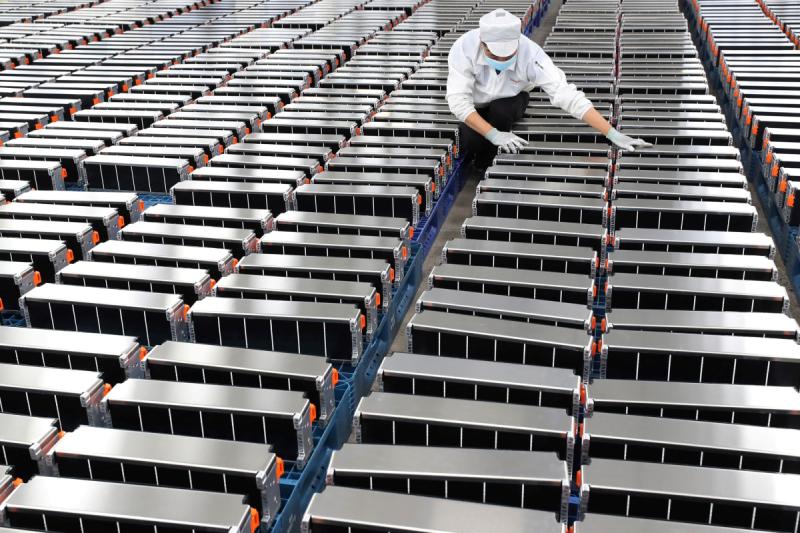
Old batteries can be hard to get rid of. However, for Ascend Elements, a recycling startup, other people’s trash is essentially a gold mine, if not better.
At the end of March, the company with headquarters in Massachusetts opened what it claims to be the largest facility in North America for recycling electric vehicle batteries in Covington, Georgia. It can handle 30,000 metric lots of info every year, separating old batteries and preparing the most important materials inside to be handled and transformed into new batteries.
That capacity likens to stall the battery packs from 70,000 electric vehicles annually, said Ascend CEO Mike O’Kronley.
As more and more people drive electric vehicles, this is an early example of a nationwide movement to recycle and repurpose EV batteries at a low cost. In earlier many years, organizations hadn’t put a lot of in lithium-ion recycling, however, investment took off over the last few years to match the spiking demand for battery materials.
Recycling can deliver new battery materials without the cost and ecological effect of new mining. New mines are extremely difficult to build in the United States, but the federal government is investing a lot of money in new battery recycling plants. Additionally, an increase in the proportion of domestically sourced batteries and battery materials is required by the revamped EV tax credits.
As a result of these shifts in the market and policy, recycling became sufficiently popular that Ascend is paying other companies for their old batteries. Currently, these deals are mostly with manufacturers of electric vehicles or batteries who need to get rid of a lot of stock.
“Paying for these spent batteries keeps them from going into the landfill,” O’Kronley told. “It’s better to get paid for it rather than throw them away.”
Additionally, batteries from battery collection programs like Call2Recycle are accepted by Ascend.
However, this does not imply that there are sufficient new batteries arriving to fill the factory. Scrap materials from battery factories, including SK Battery America’s Commerce, Georgia, plant, currently account for between 80 and 90 percent of what enters Ascend’s Covington facility.
That relationship affected Ascend’s choice of location: Covington is in the “Battery Belt,” a region of new electric vehicle and battery factories opening in the Midwest, the Carolinas, Georgia, Tennessee, and Kentucky (look for all the blue icons on this White House map of new industrial investments). Redwood Materials, a company that also recycles batteries, chose South Carolina for a $3.5 billion recycling facility.
“There will need to be a recycling plant within about an hour’s drive of every single one of those [new battery gigafactories],” O’Kronley said. “You don’t want to be [long-distance] shipping these very large, heavy EV batteries that are classified as Class 9 hazardous materials.”
As things stand, the scrap from the nearby battery factories is sent to Ascend for what’s called “pre-processing” down the road. The “black mass” is produced by mechanically shredding and sieving the used and scrap batteries. The mass is stripped of lithium carbonate by Ascend; the leftover mass contains materials like graphite, nickel, cobalt and manganese.
The majority of these substances are currently sold by Ascend to the public; it likewise changes over some black mass into cathode forerunner and cathode dynamic materials at its Massachusetts Research and development focus. However, the company is constructing a second commercial-scale facility in Hopkinsville, Kentucky, to process the Covington outputs into cathode active material and cathode precursor for use in new battery manufacturing. As part of the investment in domestic supply for crucial materials made by the Bipartisan Infrastructure Law, that $1 billion plant received $480 million in grant funding from the Department of Energy.
Similar to other battery recycling facilities, the Covington plant operates as follows: Ascend has dubbed the new method for effectively extracting cathode materials from black mass “hydro to cathode,” and it will be demonstrated at the Kentucky location.
“Those two facilities represent the investment that we are making in key infrastructure to recover these batteries, retain these critical elements in the United States and return them into the supply,” O’Kronley said.
Yet, that is only the beginning, in light of the fact that the flooding prevalence of EVs will create definitely more broken down batteries than the country’s recyclers can process. O’Kronley claims that Ascend has already begun raising funds to construct additional plants.
It’s also being done by other emerging recycling startups. JB Straubel, a co-founder of Tesla, started Redwood Materials, which got a $2 billion loan from the DOE to build a plant in Nevada to make new batteries from recycled materials. Li-Cycle, based in Canada, received a $375 million loan from the DOE to construct its own processing facility for lithium carbonate from a network of recycling plants.
These facilities tie into the Biden administration’s goal to make the U.S. more equipped for providing itself with the batteries that will be urgent to administration’s goal transportation and decarbonizing the grid.
-
Sports4 weeks ago
FIFA Club World Cup 2025: Complete List of Qualified Teams and Groups
-
Sports3 weeks ago
Al Ahly vs Inter Miami, 2025 FIFA Club World Cup – Preview, Prediction, Predicted Lineups and How to Watch
-
Health1 week ago
Back to Roots: Ayurveda Offers Natural Cure for Common Hair Woes
-
Tech2 weeks ago
From Soil to Silicon: The Rise of Agriculture AI and Drone Innovations in 2025
-
Sports3 weeks ago
FIVB Men’s Volleyball Nations League 2025: Full Schedule, Fixtures, Format, Teams, Pools and How to Watch
-
Startup3 weeks ago
How Instagram Is Driving Global Social Media Marketing Trends
-
Television4 weeks ago
Tribeca Festival 2025: Date, Time, Lineups, Performances, Tickets and How to Watch
-
Sports3 weeks ago
World Judo Championships 2025: Full Schedule, Date, Time, Key Athletes and How to Watch